Quality planning for diagnostic and medical devices
Quality by Design: quality anchored during the development and industrialization phases
The quality requirements for medical products and diagnostic products increase continuously. With our quality management we rely consistently on "Quality by Design". With this concept, this quality is no longer ensured following production by sorting out defective parts, but is instead already systematically anchored in the products and processes by our Technical Competence Center during the development and industrialization phases. The Quality Assurance department works together closely with all other involved departments during all phases of the product origin process. Quality by Design is in this way not only the securest, but also the most economical way to bring medical products and diagnostic products onto the market.
Your PLUS with Gerresheimer
Quality by design: from the idea to the series production-ready product

Our Sales and Engineering Centers and Technical Competence Centers unite all departments of product development and industrialization under one roof: Program Management, Product and process development, Mold making, Automation Engineering, Product and process development, Quality Planning and Small Batch Production. In this way we promote the intensive cooperation between Quality Assurance and the departments, and enable gap-free quality management through the entire product origin process, from the idea to the series production-ready product. In the process, we consistently rely on an integrated Quality by Design concept that reduces total costs, shortens the time to market, minimizes coordination work and reduces the risks for product and project.
Quality assurance in the Technical Competence Centers (TCC)

The Quality Assurance in the TCC encompasses the areas of Quality Laboratory and Quality Engineering. Both areas work together closely. In the Quality Laboratory, one work group each is occupied with
- material-specific, physical and chemical analyses of raw materials (plastic granulates) and damage analyses with produced components, assembly units or medical products,
- product-specific functional tests accompanying development,
- qualification and validation of the measuring devices and measurement recordings necessary for this purpose, as well as (if necessary) the method of determination.
Functional testing is formulated for both individual parts and assembly units. A test specification is thereby created for each functional test and defined in accordance with the requirements of the customer's acceptance criteria. The functional tests form the basis for the design verification of the product, which is carried out by the functional tests team. The results will then be evaluated and approved by the person responsible for the quality of the project from the Quality Engineering department.
Validation strategy / validation master plan

The thread for all of our qualification and validation activities in the project is the Validation Master Plan (VMP). The complete strategy for the qualification and validation of the production equipment, as well as the related processes, like, for example, injection mold tools, assembly lines, and measuring equipment are defined and documented here. The VMP also encompasses the validation of external processes, like, for example, sterilisation or other outsourced processes. The VMP is created by the person responsible for the quality of the project in cooperation with the other departments.
Risk management - identification, evalution and controlling of risks

Systematic risk management
- identifies, analyzes and evaluates risks that could originate from a product, medical product or component,
- evaluates the probability of occurrence, the frequency of discovery, and the severity of the risk and
- formulates reduction measures for controlling risks.
Risk management already begins at an early phase of the product origin process. The design FMEA for the product to be developed already starts in phase I. Responsible for this is the Risk Manager/FMEA moderator in the Quality Engineering area. He moderates the FMEA and heads the risk management team, which consists of one representative each from the involved departments of Product and Process Development, Mold Making, Automation Engineering, Quality and Program Management. At the earliest date possible, a representative of the production facility in which the product will be manufactured in series in the future becomes involved.
In this way, the know-how of every department is considered for the identified potential errors and their risk assessment. To start with, a risk management plan is created in correspondence with the international standard DIN EN ISO 14971 "Application of risk management to medical devices“. Besides the design FMEA, the risk consideration in the project also encompasses FMEAs for the manufacturing process (injection mold, assembly of the individual parts extending to the finished device), the packaging and potential processes for external service providers or transport. Depending upon the scope of the customer projects, the risks when using medical devices with patients in the framework of user FMEAs are also examined. We use the commercial software Scio PLATO to document the FMEA.
Qualification and validation of production equipment, processes and measuring equipment

The Quality Engineering department works together closely with the departments Mold Making (planning, design, construction, and qualification of injection molding tools) and Automation Engineering (planning, design, construction and qualification of assembly lines). The representative of Quality Engineering approves the qualification documentation created by the departments following testing and accompanies the FAT and SAT qualification runs.
Selection and qualification of measurement equipment and creation of a measurement strategy

Test measurements and critical functions are derived from the results of the design and process FMEA and flow into the test plans. Test plans for the incoming goods test, the in-process inspections and the final approval are thereby created by the person responsible for the quality of the project. A measurement strategy is then developed in cooperation with the measurement lab and the future production facility that determines which test measurements will be taken, how these should be measured and which measurement equipment (optical, tactile) are used in the process. Receptacles are planned, designed, built and qualified parallel to this for the reproducible and repeatable measurement of parts. The agreed upon measurement strategy and the qualified templates are handed over to the production facility at the handover of the project. If our customers provide technical drawings for industrialization projects, these will also be tested by quality management.
Creating the product master files (PMF)
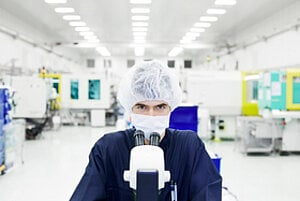
At the end of phase IV of the product origin process, the Product Master File (PMF) is handed over to the production facility following successful qualification and validation of all production equipment and manufacturing processes. The PMF is created in the Quality Engineering area. It encompasses all documents that describe the manufacture of a product. In addition to a detailed product description, the PMF contains, for example, all necessary production equipment (injection molds, assembly lines, measuring equipment) and their qualification documentation, the necessary materials and purchased parts or external services, the manufacturing processes, as well as the testing and packaging instructions. A Product Master File is created for each developed or manufactured product. Following the handing over of the PMF to the production facility, this is maintained and kept up to date by the employees in the factory during the entire product life cycle.
Design verification

The design verification is an important step in the development of a new product. It is the documented proof that all functions called for in the product specifications are fulfilled. Specific test routines are thereby formulated for each of the functions to be verified. For the design verification, a plan is created, test regulations are formulated and the test results are documented in a Design Verification Report by Quality Management in cooperation with the development department.
Small batch production

Accompanying development, initial samples can be manufactured in the Small Batch Production area. All necessary information, for example, test plans and technical drawings will thereby be handed over to Production by the Quality Engineering department. The production of sample parts, small series or batches for the product registration are monitored by an employee of Quality Management.