Customized Reusable and Disposable Pen Injectors
In the pen injector product segment, our core competence lies both in high quality, reusable pen injectors and in economically produced disposable pens, including glass cartridges. Our many years of experience in the segment of „lancing devices and lancets" is especially advantageous here. We actively look at dermatological questions like, for example, penetration behaviour and pain development. We ensure that the active ingredients of our customers, like insulin and other hormones, can be efficiently administered with little pain.
Your PLUS with Gerresheimer
Specialist for diabetes
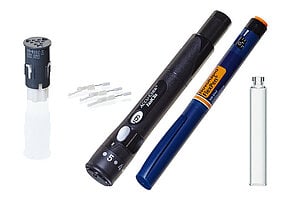
In the field of diabetes we cover the entire spectrum of diabetes products. Together with our customers we develop disposable and recyclable insulin pens for the treatment of diabetes, including the appropriate glass cartridge, as well as infusion sets for the administering of insulin. In addition to this, our portfolio also encompasses products for diabetes diagnostics like lancing devices or lancets.
Full service including glass cartridges
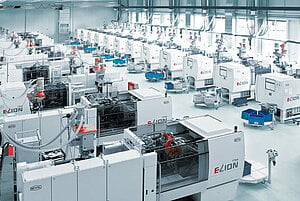
The entrance with Gerresheimer Medical Systems can be designed extremely flexibly. Are you looking for a completely new development, to further develop an existing state of development or an existing product further, or to optimize it to be plastic-compatible or to relocate production? Gerresheimer is your competent partner for product development, industrialization and contract manufacturing. Our range of services extends from concept and product development, production equipment design, mold making, special-purpose machinery through injection molding, assembly and refinement to the ready-for-sale product, including
glass cartridges. Our plastic experts work hand in hand with the glass specialists from Gerresheimer Bünde and coordinate the tolerances of glass carpules and plastic parts closely with one another. In this way we ensure that injection forces are optimized and that carpule and syringe are positioned optimally in the plastic device.
Design for Manufacturing

As a system supplier, we assume overall responsibility and carry out contract developments independently. We develop and produce your pen injector according to specifications or optimize the component layout of your concepts for the injection molding. Our experts for design and development thereby take into consideration that the Design for Manufacturing already flows into the development phase of the pen injector. For you this means a reduction in the development time, development costs and project risk, as an optimization for polymer processing after product development is no longer necessary. Quality is of the highest priority for us. Already in advance of production, the highest standards for material selection, assembly, and functionality apply.
High-tech for complex, reusable pen injectors

We utilize the entire portfolio of our technical know-how for the production of high quality, reusable insulin pens, the acceptance of which in the routine of patients ultimately depends not least upon attractive design: Laser welding of metal parts, laser welding and laser labeling of plastic parts and painting processes fulfill the strictest requirements for technical and visual quality. Our internal Automation Engineering department conceives of and builds assembly systems with which the necessary extremely precise feed of plastic and metal parts is possible at high speeds. Production in the clean room is self-explanatory for us. We also ensure the optimal surface quality and functional safety of the products through assembly that is gentle with the visible surfaces and visual inspection for damage to the visible parts within the assembly system. A 100% in-process inspection of the assembly steps, of the assembly units and product functions takes place with a large number of intelligent camera systems and inspection stations in the assembly system
Economically produced disposable pens

We produce disposable pens for insulin and other hormones in numbers of units exceeding 350 million per year. Here we ensure the most economical production possible through highly automated assembly processes and systems for pad printing coupled directly with the injection molding machine.
Samples for clinical test studies, development samples, and stability batches

Before a drug delivery device or a medical technology device can enter into series production, it must first run through an exhaustive approval process. In this phase it is often not yet certain where the final production location will be. Nonetheless, a small number of products is always required again and again, even at this point in time, for example, as samples for clinical studies, development samples, or for stability batches. In order that our customers receive these products quickly, in an uncomplicated way, and, most importantly, at a high level of quality, we have set up our own small batch production at our Technical Competence Center (TCC) in Wackersdorf. The TCC is equipped with a clean room in accordance with ISO 14644-1 ISO class 8 with injection molding machines, project-specific assembly systems like automatic joining systems, gluing apparatus or systems for ultrasonic welding and automatic testing systems.
Qualification and validation

All relevant standards and regulations are of course taken into consideration for the qualification and validation of the pen injectors: GMP guidelines (GxP), GAMP5 guidelines, 21 CFR Part 820, 21 CFR Part 11, ISO 9001, ISO 13485, MDD 93/42/EEC, AMG/MPG/AMWHV.
Worldwide production capacities
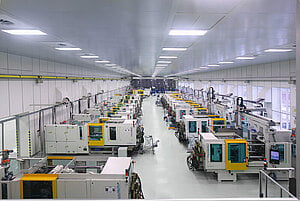
We offer our customers 120,000 sqm (1,300,000 sqft) of production area, of which around 60,000 sqm (670,000 sqft) is clean room area in accordance with ISO 14644-1 ISO classes 7, 8, 9 and GMP classes C and in Pfreimd (Germany), Horšovský Týn (Czech Republic), Skopje (North Macedonia), Peachtree City (USA), Indaiatuba (Brazil) and Dongguan City (China).